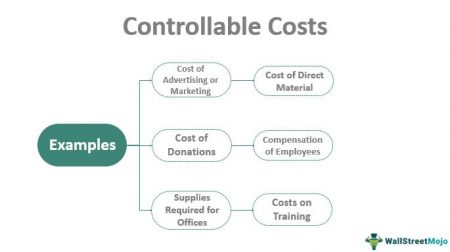
Elements of manufacturing costs In manufacturing organizations, the calculation of three elements: direct materials, direct labour head. For stock valuation the costs of a product.
- Direct materials xxx xxx xxx xxx xxx
- Direct labour xxx xxx xxx xxx xxx
- Prime cost xxx xxx xxx xxx xxx
- Manufacturing overhead xxx xxx xxx xxx xxx
- Total manufacturing cost xxx xxx xxx xxx xxx
Direct materials consist of all those materials that can be physically identified with a specific product. For example, wood that is used to manufacture a desk can easily be identified as part of the product, and can thus be classified as direct materials. Alternatively, materials used for the repair of a machine that is used for the manufacture of many different desks are classified as indirect materials.
These items of materials cannot be identified with any one product, because they are used for the benefit of all products rather than for any one specific product. However, not all items of materials that can be identified with a specific product are classified as direct materials. For example, the nails used in the manufacture of a particular desk can be identified specifically with the desk, but, because the cost is likely to be insignificant, the expenses of tracing such items do not justify the possible benefits from calculating more accurate product costs.
Note that indirect materials form part of the manufacturing overhead cost.
Elements of Manufacturing Costs
Direct labour consists of those labour costs that can be specifically traced to or identified with a particular product. Examples of direct labour costs include the wages of operatives who assemble parts into the finished product, or machine operatives engaged in the production process. By contrast, the salaries of factory supervisors or the wages paid to the staff in the stores department cannot be specifically identified with the product, and thus form part of the indirect labour costs.
The wages of all employees who do not work on the product itself but who assist in the manufacturing operation are thus classified as part of the indirect labour costs. As with indirect materials, indirect labour is classified as part of the manufacturing overhead cost.
Prime cost refers to the direct costs of the product and consists of direct labour costs plus direct material costs plus any direct expenses. The cost of hiring a machine for producing a specific product is an example of a direct expense.
Manufacturing overhead consists of all manufacturing costs other than direct labour, direct materials and direct expenses. It therefore includes all indirect manufacturing labour and material costs plus indirect manu-facturing expenses. Examples of indirect manufacturing expenses in a multi-product company include rent of the factory and depreciation of machinery.
To ascertain the total manufacturing cost for stock valuation, all that is required for the direct cost items is to record the amount of resources used on the appropriate documents. For example, the units of materials used in making a particular product are recorded on a stores requisition, and the hours of direct labour used are recorded on job cards. Having obtained the quantity of resources used for the direct items, it is necessary to ascertain the price paid for these resources.
The total of the resources used multiplied by the price paid per unit of resources used provides us with the total of the direct costs or the prime cost for a product. In contrast, it is not possible to attach overhead costs accurately to products, since overhead costs are incurred for the benefit of all products, and the amount of the overheads that should be allocated to a specific product can only be an estimate.
The accountant resolves this problem by ascertaining the total overheads for a period and then sharing these costs among the products that have been manufactured during the period, on some sensible basis.
The distinction between direct and indirect costs depends on the cost objective. We have assumed in this section that the cost objective is the product for stock valuation. Costs are classified as direct or indirect, depending on their traceability to the cost objective. If the cost objective is to establish the cost of using various distribution channels for decision-making then the rental of warehouses and the salaries of storekeepers will be regarded as direct costs for each distribution channel.
These costs, however, cannot be directly traced to products, and are therefore indirect for stock valuation purposes. Similarly, for control the cost objective may be to compare the costs incurred in obtaining customers’ orders with budgeted costs.
In this situation salesmen’s salaries and travelling ex-penses will be regarded as direct costs, whereas the costs of the personnel department in appointing production, administration and sales staff will not be traceable to the cost objective. Consequently, these costs are indirect. In other words, a direct cost is a cost which can be specifically identified with a cost objective.
Job and process costs.
For stock valuation we have noted that the manufacturing cost must be calculated for each unit of output. In an organization that produces a wide range of products or jobs, and where each order is unique and requires different amounts of labour, material and overhead, the cost of each order must be calculated separately. Such a cost accumulation system is known as a job costing system.
An alternative cost accumulation system known as process costing can be applied to an organization that produces many units of the same product during a period. With a system of process costing, the allocation of manufacturing cost to a specific order is unnecessary. Instead, the cost of a single unit can be obtained by merely dividing the costs of production for a period by the number of units produced in that period. In other words, the cost of an order is assumed to be the average cost per unit of all the units that have been produced during the period multiplied by the number of units ordered.
Job costing classification is suited to industries that produce specialized or made-to-order outputs. Examples of such industries include construction, printing, machinery and shipbuilding. Because each customer’s order is normally unique, average costs per unit of output are not suitable. A job costing system give a more accurate calculation of product costs because costs are accumulated for each specific order, but the system is expensive in terms of the clerical work involved in attaching direct costs to each specific job.
Leave a Reply